Plastic extrusion for extra-durable, resilient materials
Plastic extrusion for extra-durable, resilient materials
Blog Article
Understanding the Basics and Applications of Plastic Extrusion in Modern Production
In the realm of contemporary production, the technique of plastic extrusion plays a critical role - plastic extrusion. This complex procedure, involving the melting and shaping of plastic with specialized passes away, is leveraged across different markets for the production of diverse products. From vehicle components to durable goods packaging, the applications are substantial, and the possibility for sustainability is similarly outstanding. Deciphering the basics of this process discloses real adaptability and potential of plastic extrusion.
The Basics of Plastic Extrusion Process
While it may appear complex, the basics of the plastic extrusion procedure are based on relatively straightforward concepts. It is a manufacturing process where plastic is thawed and afterwards formed into a continuous profile via a die. The raw plastic product, frequently in the form of pellets, is fed right into an extruder. Inside the extruder, the plastic goes through warm and pressure, triggering it to melt. The molten plastic is then compelled via a shaped opening, recognized as a die, to form a long, constant product. The extruded item is cooled and after that reduced to the wanted size. The plastic extrusion process is thoroughly utilized in numerous markets due to its versatility, cost-effectiveness, and effectiveness.
Various Kinds Of Plastic Extrusion Techniques
Structure upon the standard understanding of the plastic extrusion procedure, it is essential to explore the numerous strategies involved in this manufacturing approach. The two key techniques are profile extrusion and sheet extrusion. In account extrusion, plastic is thawed and created into a continual account, typically made use of to develop pipelines, poles, rails, and home window frames. In comparison, sheet extrusion creates big, level sheets of plastic, which are normally more refined right into products such as food packaging, shower drapes, and cars and truck components. Each strategy requires specialized machinery and accurate control over temperature level and pressure to guarantee the plastic preserves its visit their website form throughout cooling. Recognizing these methods is crucial to utilizing plastic extrusion successfully in modern-day production.
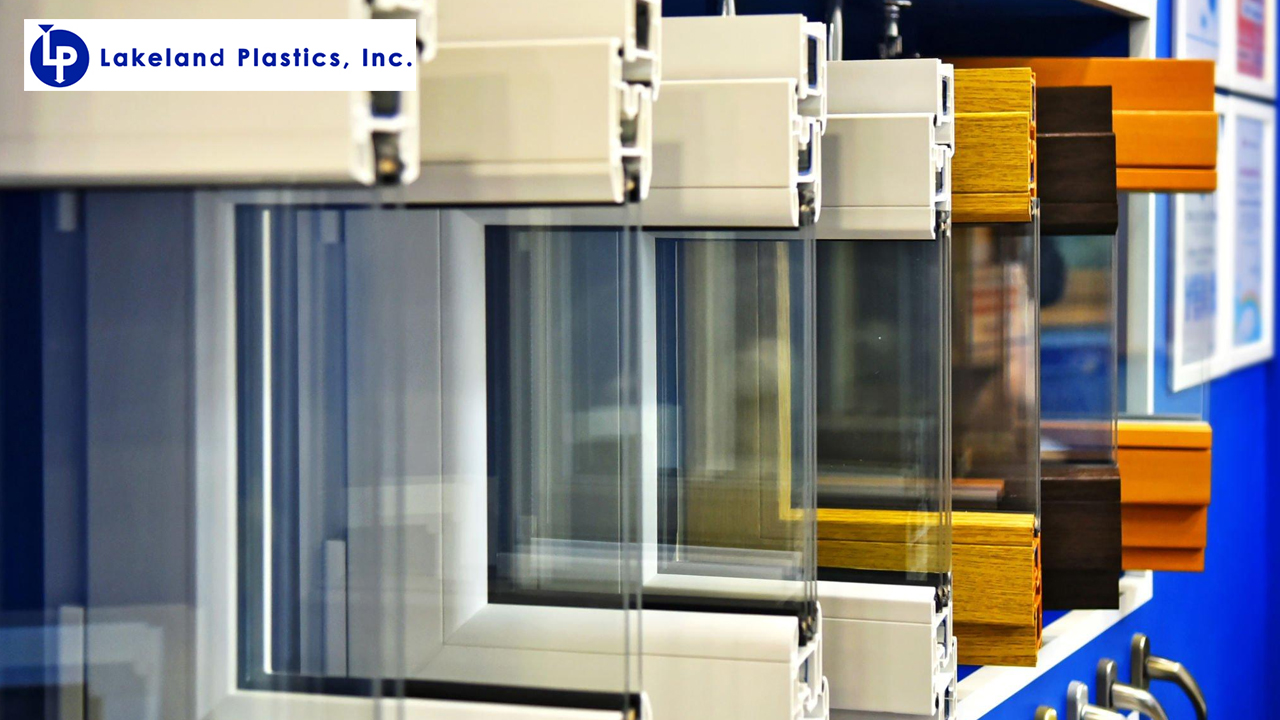
The Role of Plastic Extrusion in the Automotive Sector
A frustrating majority of parts in modern cars are products of the plastic extrusion process. Plastic extrusion is mostly utilized in the manufacturing of numerous auto elements such as bumpers, grills, door panels, and dashboard trim. Therefore, plastic extrusion plays an essential duty in automotive manufacturing.
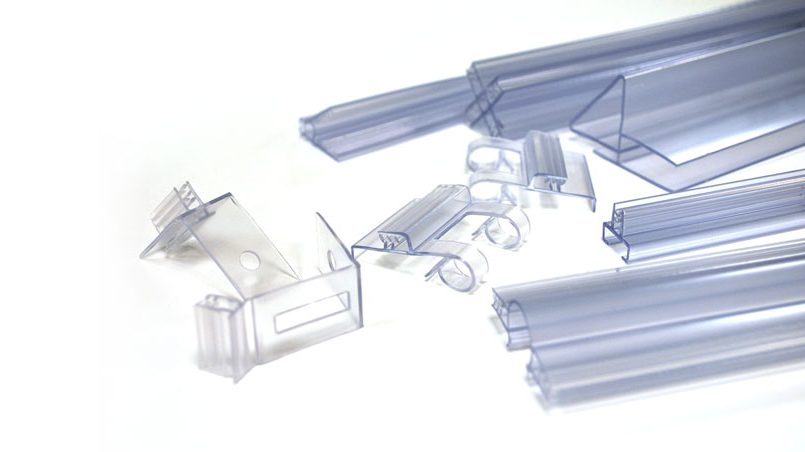
Applications of Plastic Extrusion in Durable Goods Manufacturing
Past its substantial impact on the vehicle industry, plastic extrusion shows similarly reliable in the realm of consumer products making. The flexibility of plastic extrusion enables suppliers to design and create intricate forms and sizes with high precision and effectiveness. The adaptability, versatility, and cost-effectiveness of plastic extrusion make it a recommended selection for many consumer products makers, adding considerably to the market's growth and technology.
Ecological Impact and Sustainability in Plastic Extrusion
The pervasive usage of plastic extrusion in manufacturing welcomes scrutiny of its eco-friendly implications. Reliable machinery reduces power use, while waste monitoring systems recycle scrap plastic, decreasing raw material demands. Regardless of these enhancements, additionally technology is required to reduce the environmental impact of plastic extrusion.
Conclusion
To conclude, plastic extrusion plays an important role in modern-day manufacturing, particularly in the automotive and durable goods markets. Its flexibility enables the manufacturing of a broad array of components with high accuracy. More hints Moreover, its capacity for reusing and growth of naturally degradable products provides an appealing avenue towards lasting techniques, thus resolving ecological issues. Recognizing the basics of this process is essential to maximizing its advantages and applications.

The plastic extrusion procedure is thoroughly utilized in various sectors a fantastic read due to its effectiveness, cost-effectiveness, and flexibility.
Structure upon the fundamental understanding of the plastic extrusion procedure, it is essential to check out the different techniques entailed in this manufacturing technique. plastic extrusion. In contrast, sheet extrusion develops big, level sheets of plastic, which are normally additional refined right into products such as food product packaging, shower curtains, and auto parts.A frustrating majority of parts in modern-day cars are products of the plastic extrusion process
Report this page